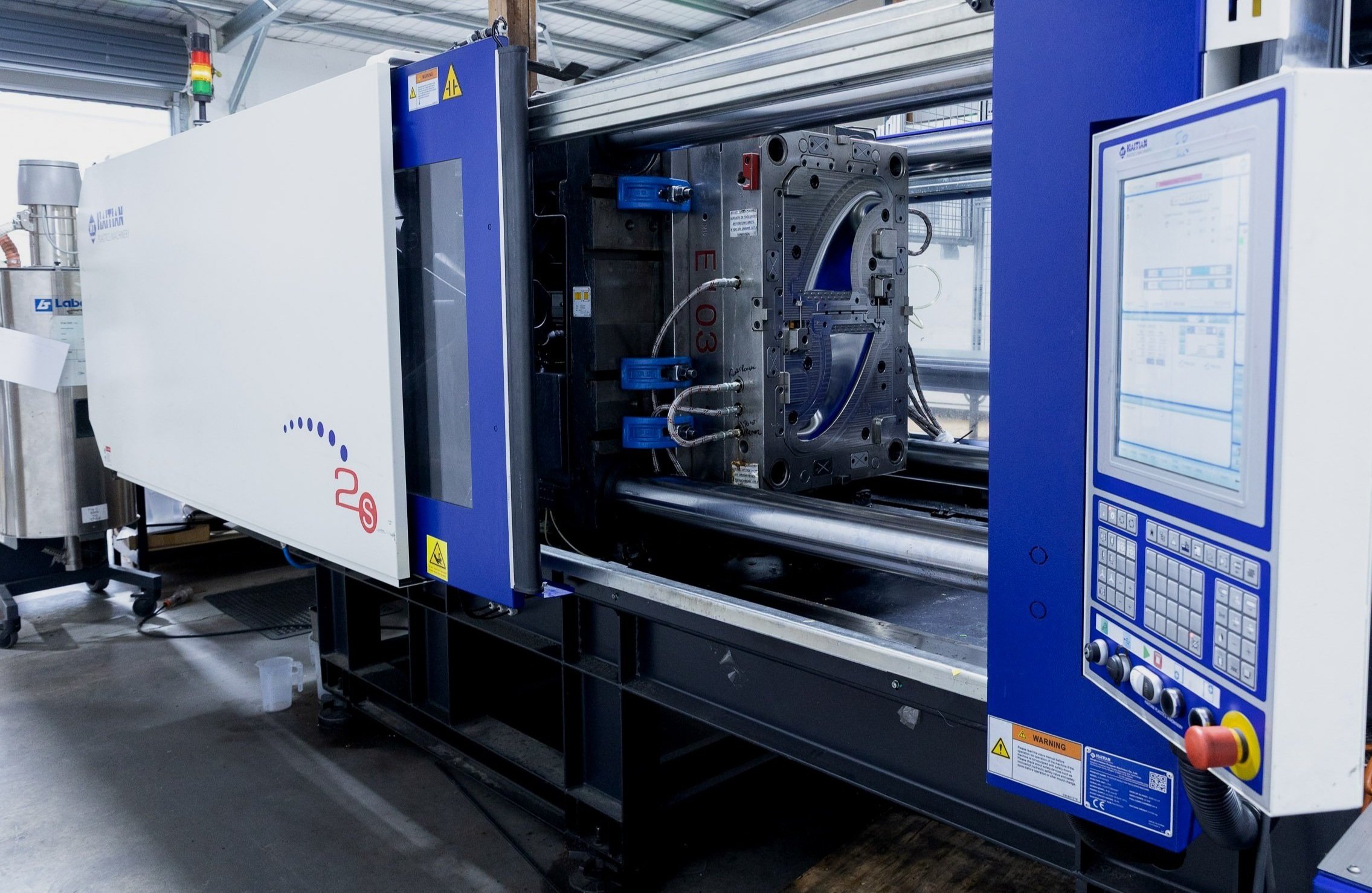
Injection Moulding
A diverse range
of products
Injection moulding is a manufacturing process in which molten material is injected into a mould cavity under high pressure to create precise, high-volume parts, typically made from plastic, with complex shapes and intricate details.
The plastic moulding process offers high efficiency and speed, exceptional precision and consistency and remarkable design flexibility. Injection moulding is highly automated and a cost-effective option for large-volume production.
At NTD we mould a wide range of engineering and commodity plastics in shot weights from a few grams to 1.5 kilograms, including PA, POM, PC, PP, ABS, AES, ASA, PE, TPU, TPE, PSO, HIPS, PVC and PBT.
Cutting Edge Technology
Over the past few years, we’ve made significant investments in cutting-edge technology, with 11 of our 14 moulding machines brand new. Our machines feature a combination of full-electric, electric hybrid and hydraulic systems, with clamping forces ranging from 50 to 380 tonnes.
To enhance operational efficiency and productivity, we’ve integrated 3-axis robots into our new machines, with plans to add even more. Raw materials are automatically fed into the machines via hopper loaders, while finished products are seamlessly placed on conveyors, further boosting our level of automation.
Manufacturing Options
Over moulding is a multi-shot injection moulding process that produces a single product from two or more different thermoplastics. The first “shot”, known as the substrate, is typically the more rigid of the two materials and is designed to accept the subsequent shots/over-moulds.
A variety of thermoplastics can be used for the over-mould, but they’re usually softer and more flexible than the substrate. The over-mould material may be mixed with colourants, foaming agents, and other additives to achieve the desired effect upon completion. Over-moulding typically allows for cosmetic differentiation in a part while also enhancing tactile performance.
Insert moulding is a specialised injection moulding process in which metal components—such as nuts, bolts, threaded bushings, or other reinforcing elements—are placed into the mould cavity before the plastic is injected. During the moulding cycle, molten plastic flows around the pre-positioned inserts, encapsulating them within the finished plastic part to create a strong mechanical bond. This method eliminates the need for secondary assembly steps, improving production efficiency and part strength.
These inserts can be stainless steel, brass or steel. Knurled brass inserts are commonly used as they provide excellent retention within the moulded plastic.