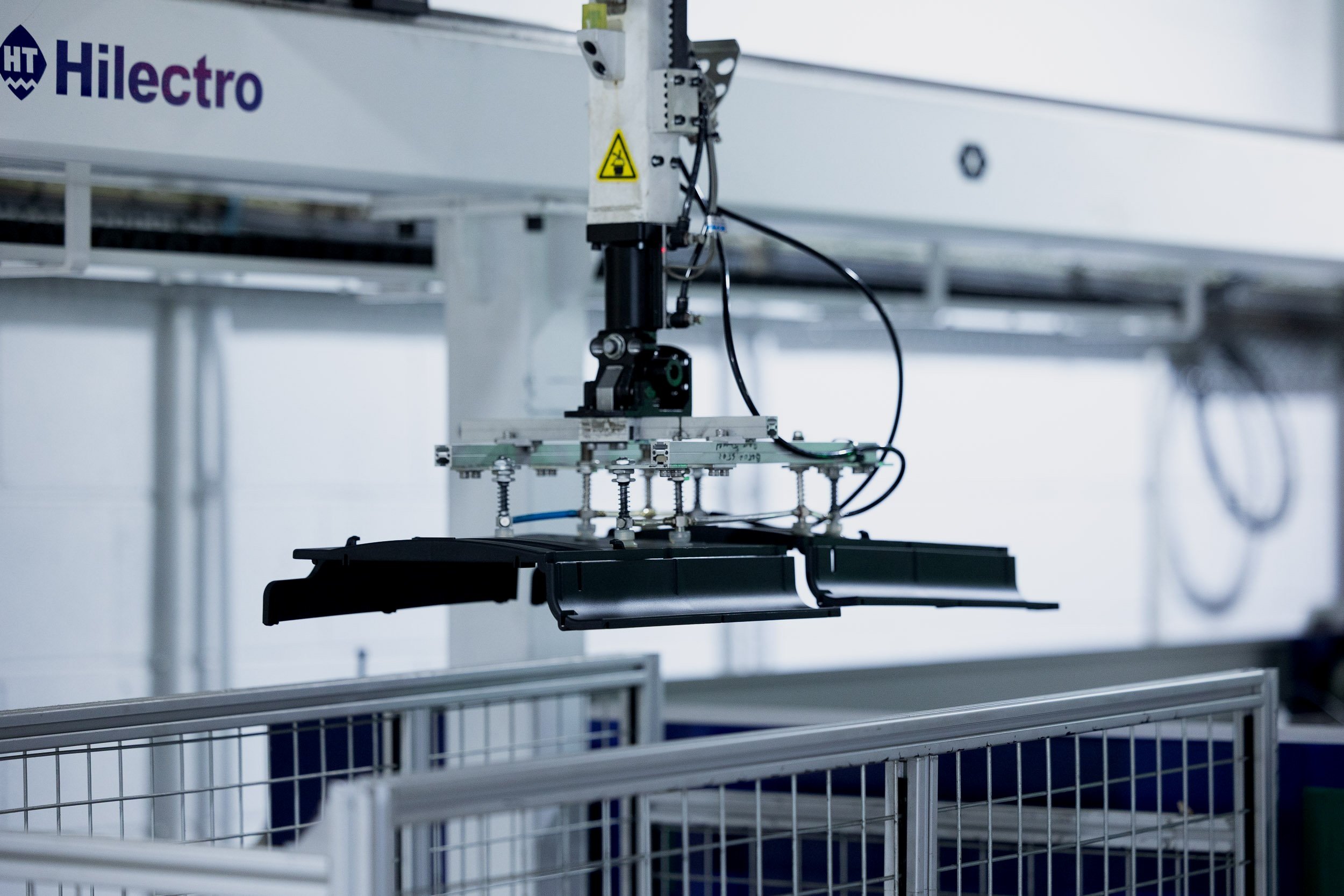
Product Design
Cutting-edge software and advanced simulation
At NTD, we combine cutting-edge software, in-house tooling expertise, and advanced simulation to deliver smarter product design solutions. Whether you're starting with a concept sketch or a fully defined brief, our experienced engineering team ensures your product is ready for efficient, high-quality production.
Smart Design with SolidWorks + CamWorks
We use SolidWorks—the industry-leading 3D CAD software—to develop complex, precision-engineered designs for injection moulded parts. From the smallest detail to complete mould assemblies, SolidWorks allows us to model with speed, accuracy and efficiency.
Our designs flow directly into CamWorks, our computer-aided machining (CAM) software, creating a seamless link between design and manufacture. This integration lets us generate machining code quickly and accurately, reducing lead times and ensuring the final tool is exactly as designed.
Expert In-House Tool Design
Great injection moulding products start with great tooling. At NTD, our in-house tool designers take a holistic approach to every project—considering not only the product itself, but also how it will be produced, assembled, packaged and delivered.
We assess key factors such as part geometry, material and function, process choice, surface treatment, assembly and delivery logistics.
Using tools like Moldflow, Failure Mode and Effects Analysis (FMEA) and tolerance analysis, our team collaborates closely with prototyping and manufacturing to design tools that reduce manufacturing costs, improve quality and speed up time to market.
Rapid Prototyping for Faster Feedback
Our in-house 3D printing capabilities help accelerate design validation and reduce the risk of rework. We produce functional prototypes early in the development process—allowing you to evaluate form, fit and performance before committing to tooling.
Through our trusted partner network, we also offer a range of advanced prototyping technologies, including Fused Deposition Modeling (FDM), Stereolithography (SLA), Selective Laser Sintering (SLS), Direct Metal Laser Sintering (DMLS), and Multi Jet Fusion (MJF). This is complemented by a wide range of materials and surface finishes to optimise design detail and product performance.
Moldflow Analysis: Design Backed by Data
We use Moldflow, the industry’s leading plastics simulation software, to accurately predict how your chosen material will flow within the mould—long before any steel is cut. This advanced analysis gives our engineers critical insight into every aspect of the injection process including fill time, pressure, temperature distribution, and potential sink or quality issues.
With this data, we can validate and refine your part design, trial alternative polymers and recommend adjustments to geometry or material selection early in the process. Moldflow also enables us to optimise feed systems in family moulds, fine-tune process parameters and conduct detailed cooling analyses. We can even predict part warpage and implement corrective actions before production begins.